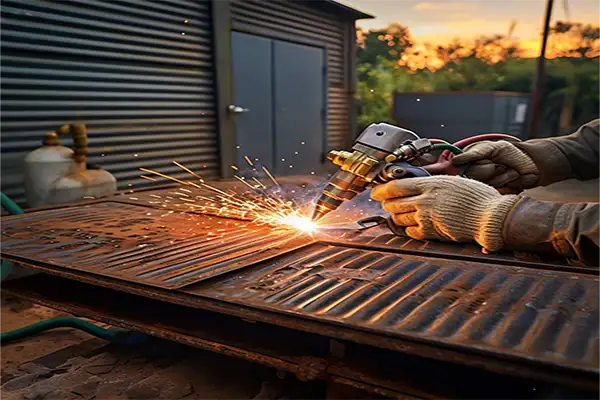
Существует большое количество типов резки и обработки материалов разной природы помимо металлических изделий. Они отличаются по типу используемого инструмента, с помощью которого осуществляется резка. При этом их можно разделить на две большие группы – ручной и станочный инструмент. К первому типу относятся инструменты, применимые для в быту, – это болгарка, лобзик, пила и т.д. – все, что выполняет режущую функцию. Второй тип инструмента используется на производствах, входит в состав практически полностью автоматизированных станков. И вот этих станков может быть достаточно много, чтобы застрять при выборе наиболее оптимального из них. Потому что у каждого вида резки есть, как и плюсы, так и минусы. В этой статье речь пойдет о газовой резке, об ее особенностях, а также какое оборудование для этого используется. Давайте разбираться, как работает газовая резка.
Механизм газовой резки
Считается, что самыми дешевыми технологиями для обработки металлических и любых других изделий являются гидроабразивная и газовая резки. Из-за того, что не требуется особое специализированное оборудование: не нужно резцов, фрез, лазеров. Это значительно упрощает техобслуживание и сокращает статью расходов на него. При том для газовой резки не нужно будет закупать песок в крупных масштабах, как для гидроабразивной резки. И вообще ее можно выполнять вручную.
Очевидно, что в технологическом процессе газовой резки самым важным инструментом выступает газ. Наиболее распространен кислород и газовые смеси на его основе. В процессе работы лист металла греют до высокой температуры – около 1000°С, затем под давлением через сопло подается струя кислорода, который резко воспламеняется при контакте с раскаленной поверхностью. Струя легко режет материал, если газ подается непрерывно. Здесь важно, чтобы металл не плавился раньше времени. Под действием горящего кислорода он должен моментально сгорать, за счет чего и происходит резка. Образующиеся наплавы достаточно сложно удалять. Важно отметить, что нагрев металла осуществляется в локальных местах, определенной площади.
Данный тип резки наиболее подходящий для обработки крупногабаритных деталей, потому что не всегда экономически выгодно изготавливать их механическими и другими способами. Изготовление таких деталей на лазерном оборудовании может влететь в копеечку.
Классификация
Газовая резка относится к термическим способам металлообработки, при этом может быть поделена на два вида в зависимости от назначения и мощности оборудования. Это разделительная и поверхностная резки. Первый применяется для разделения, второй – для гравировки. Соответственно, мощности инструментов в том и в другом случае будут разными.
Тип режущего оборудования подбирается индивидуально в зависимости от заявленных характеристик конечного изделия. Ниже в таблице представлены самые распространенные и экономически выгодные для использования.
Режущий инструмент | Особенности |
---|---|
кислород-пропановая смесь | самый популярный; не применим для резки высокоуглеродистых сплавов; возможно использовать другие низкомолекулярные газы |
кислородная дуга | подходит для гравировки поверхности; не особо эффективна для листов большой толщины |
кислородно-флюсовая смесь | добавление порошкового флюса, обеспечивающего большую пластичность материала |
кислородно-копьевая резка | повышенная скорость и мощность резки |
Преимущества и недостатки
Самым главным плюсом газовой резки, как уже было отмечено, является соотношение качества и дешевизны оборудования. Тот факт, что таким способом резать металл можно даже в полевых условиях, дает огромное преимущество перед всеми остальными видами металлообработки. Также следует отметить универсальность газовой резки. Исходный материал может быть любой толщины, а фигурность – любой сложности.
Из недостатков можно выделить следующее:
- значительный термический нагрев;
- взрывоопасность газа;
- низкая мощность для выполнения особо точных работ;
- деформация металла (плавление).
Важно все это учитывать при работе с газовыми приборами или станками и своевременно проводить диагностику, чтобы избежать нежелательных последствий.