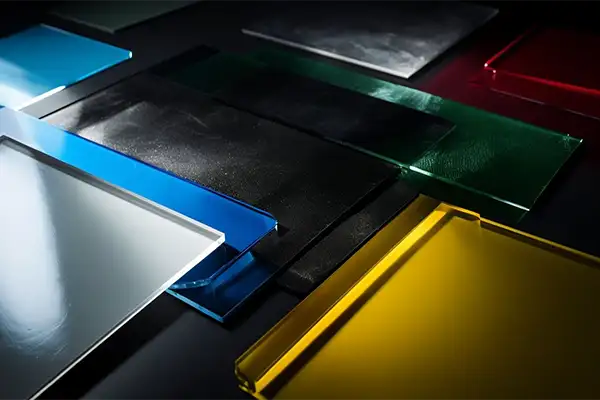
Одной из востребованных направлений в пластмассовой отрасли по сей день остается обработка полимеров с использованием специализированного оборудования и инструмента. На таком оборудовании можно пластмассу как обрабатывать, не нарушая целостность, так и производить что-то новое, отличное от исходного. Таким образом ее можно резать, пилить, сверлить, гравировать, а также плавить, сваривать, перерабатывать и смешивать между собой.
Одним из интересных направлений переработки является производство листовой пластмассы. Для этого используются технологии процессов вальцевания и каландрования. Как известно, вальцевание также применяется для изготовления металлических листов. Каландрование же в основном используется для резины и пластмассы. Далее кратко обозначим, что такое вальцевание и каландрование, а также какое оборудование для этого используется.
Вальцевание
На пластмассовом производстве процесс вальцевания используется для изготовления тонких листов, но чаще всего для пластификации и смешения полимеров. Пластификация подразумевает введение в общую массу полимеров с малым молекулярных весом, которые придают большей пластичности. Смешение осуществляется с целью гомогенизации смеси. После процедуры листовой полимер становится более гладким и пластичным.
Вальцевание осуществляется на специализированных станках, оснащенных валками, которые непрерывно крутятся навстречу друг другу. Массу полимера и необходимые для смешения компоненты подаются на валки, которые крутятся навстречу друг другу, нагревая их. Нагрев происходит за чет трения частиц между собой. После смешения резина прилипает к одному из валков, затем слой срезается и процесс смешения повторяется несколько раз. Валки можно разделить на валки непрерывного и периодического действия. Валки непрерывного действия обычно принимают полимерную смесь, налипание слоя осуществляется на валки периодического действия. Либо компоненты сразу направляются в зазор между ними. Также, в том числе, смесь может налипать на оба валка сразу и непрерывно сниматься, далее направляясь обратно в зазор.
Итого в конце всего процесса получается длинный лист резины или пластмассы, свернутый в рулон. Компоненты сырья хорошо перемешаны и однородны, при этом рулон все еще теплый и готов к дальнейшей обработке каландрованием. Здесь важно отметить, что таким образом обрабатываются только термопласты, которые могут плавиться при нагревании.
Каландрование
Каландрование – это следующий процесс прокатки листовой резины. Такой станок тоже оснащен валками, которые действуют по тому же принципу, что и в процессе вальцевания. Валков должно быть более двух. Один как правило имеет максимальную температуру, а другой минимальную. Эта особенность работы валков обеспечивает равномерный переход массы полимера. На выходе получается готовый и ровный полимерный лист, также свернутый в рулон. При этом такой лист обладает заданной толщиной и глянцевой поверхностью. Важная особенность в том, что полученный таким образом полимерный лист становится более прочным за счет удаления пузырьков воздуха при неоднократной прокатке.
Следует выделить несколько важных требований, предъявляемых к термопластам, за соблюдением которых важно следить, чтобы получить качественный полимерный лист.
- Полимер должен быть высокоэластичным в определенном диапазоне температур, в этом диапазоне должны работать каландры.
- Полимер должен хорошо сцепляться с материалом валков, что необходимо для перемещения листа с одного валка на другой.
- Полимер не должен разрушаться при снятии с валка.
- Полимер должен быть стабилен в определенном диапазоне температур.
Все эти свойства полимера как правило закладываются еще на этапе вальцевания при смешивании компонентов. Но также необходимо регулировать работу каландров.
Пленки, полученные процессом вальцевания-каландрования, могут быть толщиной от 0,5 до 1 мм. Именно такой ширины чаще всего устанавливают зазор между валками. Такие пленки гораздо более ровные и однородные по толщине, чем, например, полученные экструзией.